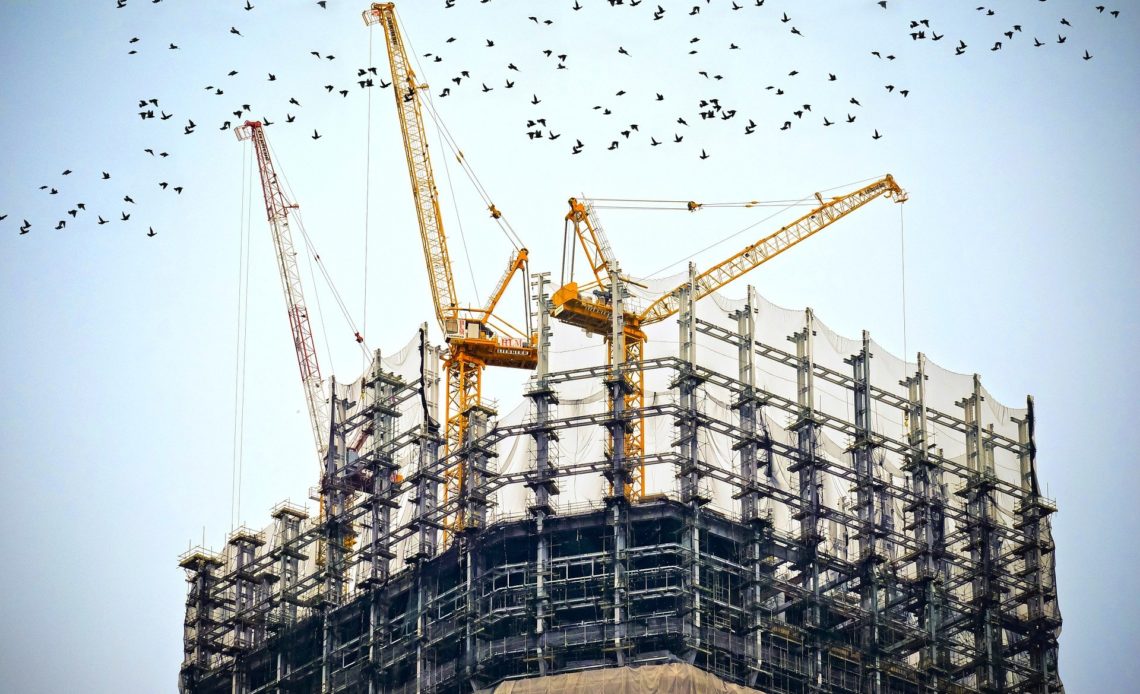
Productivity growth on construction sites has lagged the overall economy for decades. High costs of construction have a ripple effect on the expenses of manufacturing and the rest of the economy. The construction industry copes with enormous challenges of coordination which are a drag on productivity. They communicate with Architecture and Engineering companies (AEC) to align blueprints and drawings with the physical reality of construction. Additionally, building sites coordinate with materials suppliers to ensure adequate on-site inventory and enough is in transit to meet ongoing needs. Miscommunication in construction sites is rife as the details of the specifications of architects are hard to match with the reality of construction progress. Unexpected events could also interrupt the flow of building materials and delay the construction progress.
Productivity can grow with 3D imagery
According to McKinsey, the rate of growth of productivity in construction for the last two decades has been a measly 1 percent compared with an increase of 2.8 percent for the total world economy and 3.6 percent in the case of manufacturing. Digital representation of designs with 3D modeling began in the aerospace industry in the 1970s and boosted productivity by ten times. The construction industry, by contrast, has introduced 3D building information models in design but rarely integrates project planning, design, construction, operations, and maintenance. Digital twins will play a vital role in the integration of processes across a construction site.
Real-time communications between construction sites, AECs, and suppliers are needed to align design with construction progress. They operate from several different locations. On-site personnel scattered around multiple ends of the construction site add to the complexity. For real-time communications, they need visual tools to see what each of them sees in real-time data. They can then superimpose the virtual copy of the design onto the actual world and spot anomalies that they could correct and prevent them from getting baked into the building.
Currently, the big video and virtual reality files that construction workers download take excessive time to an extent where they could lose the latest update. 5G is starting to bring the connectivity the construction industry needs for real-time downloads. In addition, data from sensors will keep track of the state of progress on the site, such as the state of the concrete setting and materials in transit for project planning.
Private networks and construction sites
One of the first 5G deployments of Ericsson-acquired Cradlepoint had its Enterprise Wireless solution for an Australian construction company Taylor Construction. The client had already started using the Microsoft HoloLens, a mixed-reality wearable, but found that their 4G network bandwidth was inadequate.
Taylor Construction also embeds sensors in the bars that act as enclosures for wet concrete to track construction progress, update the information on building blueprints, and display them on HoloLens. Streaming video from cameras on-site informs the architects in Sydney about the state of progress. The 5G network has improved performance 20x over 4G using Telstra’s 3.5 GHz spectrum.
Microsoft Azure Digital Twins is taking the initiative to create an ontology (categorization) of construction activities in collaboration with a Swedish real-estate consortium, RealEstateCore. The ontology will be a foundation for sharing of data among owners, construction companies, and vendors. In addition, digital Twins will be the means to represent the data virtually for finding ways to reap higher value from the services added to buildings and for cost control during and after construction. For example, by drawing on data from building controls, Microsoft reduced energy consumption by 20-30%.
In addition, the knowledge repository, created during construction, has lasting value with its interlinking with the digital twin; it can visually show how to install a piece of equipment and plan for maintenance.
Conclusion
Low productivity during construction has several ripple effects that increase costs for the economy and leave its imprint for the rest of the life of the building, affecting its maintenance and ability to adapt to future needs. Communication technologies such as X-Reality boost productivity by speeding up coordination among the diversity of parties involved in construction. The knowledge base created to rationalize construction has impacts throughout the lifecycle of the building. It helps to troubleshoot when some equipment or structure in the building breaks down. It leaves a record of the activities during construction that provides insights to diagnose problems and find solutions that progress as new technologies emerge.